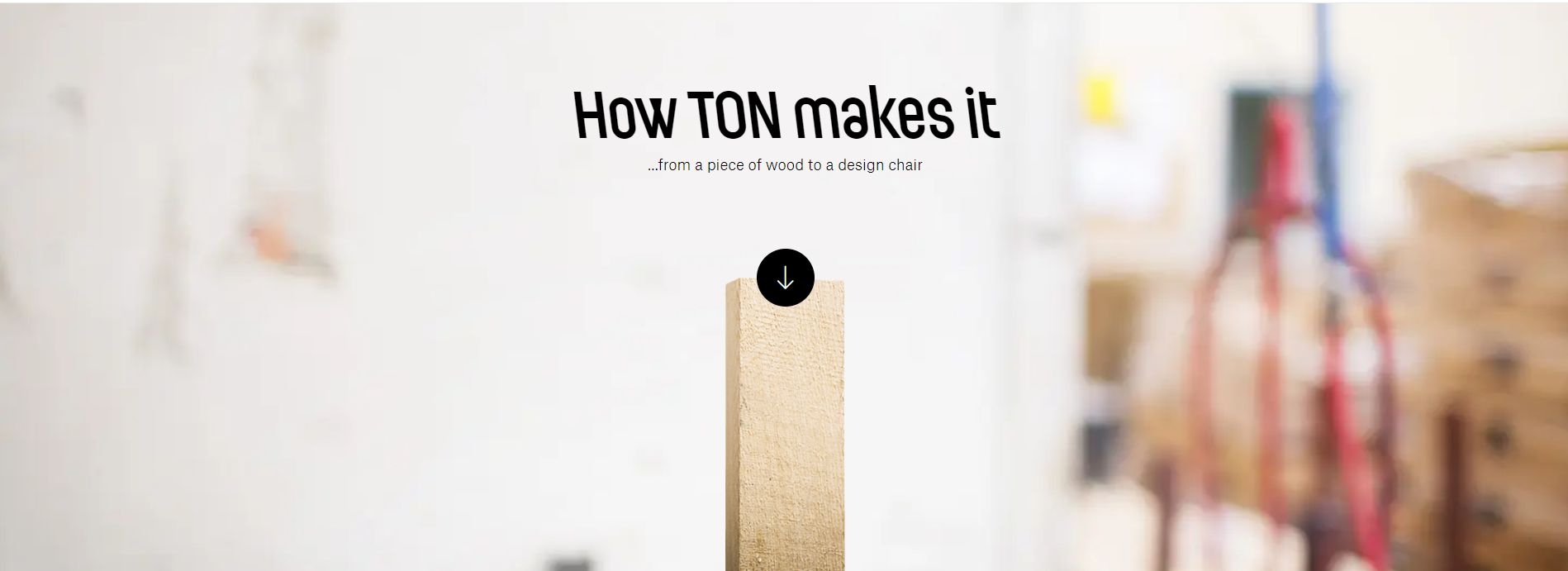
1. Laser cutting
We stock almost 50 types metal tube in our warehouse.We grade them by surface,diameter and thickness of the tube.This procedure is necessary for the material to stock to avoid mistake in materials. And our factory is near to the metal tube factory suppliers,which could us reach metal tubes as soon as we received the orders from clients. We have 5 CNC automatic laser cutting machines, which increase the possibility of cutting different sections, improve the precision of cutting, improve the efficiency, and at the same time, reduce the cost to a certain extent.
(1) The use of the most advanced professional software provides the possibility of cutting various designs of different sections
(2) Due to advanced programming technology, laser tube cutting can efficiently complete the work in one step, saving more time and reducing costs for mass production. Fully automatic It can realize automatic cutting of batches of pipes without human intervention without human intervention. The humanized design of the whole machine makes the best use of raw materials while improving the cutting efficiency, reduces production costs, and achieves "0" tailings.
(3) Compared with traditional manual cutting and outdated machine precision cutting, our machine has better 0.1mm automatic cutting precision. There will be no burrs, the surface is smoother, and the later welding effect is better.
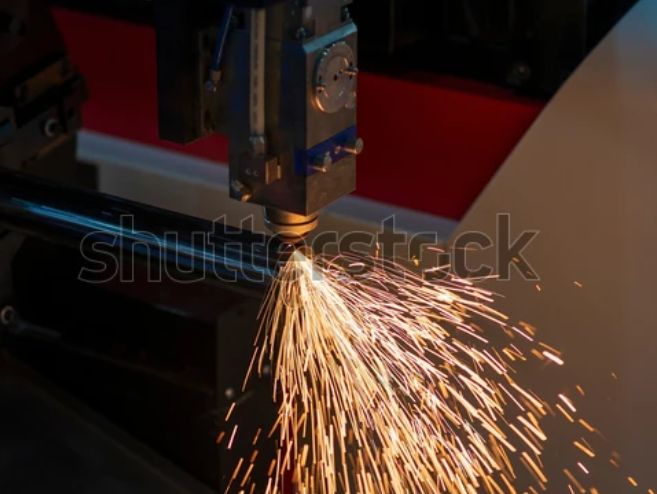
2. CNC tube bending
After tube cutting process, the tubes will be move to another production line-our CNC tube bending machines. By importing or importing pipe geometry data directly from a CAD 3D file and the equipment automatically creates and executes the equipment program.
Perfect curves are achieved even with small radii. At the same time, the use of reels simplifies material flow and eliminates semi-finished products to be stored and handled, as well as intermediate steps in workpiece processing on other equipment. Improve the effect and reduce the cost.
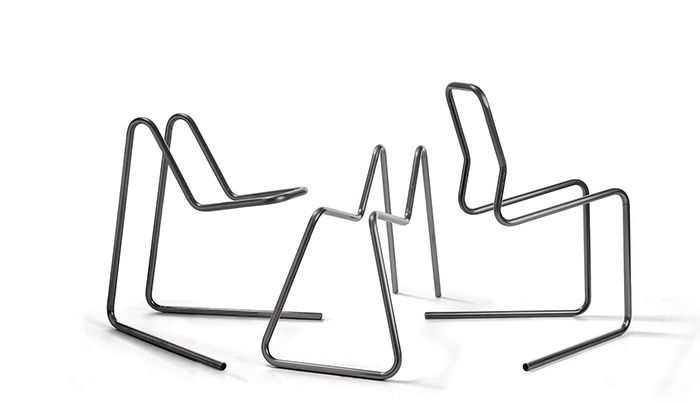
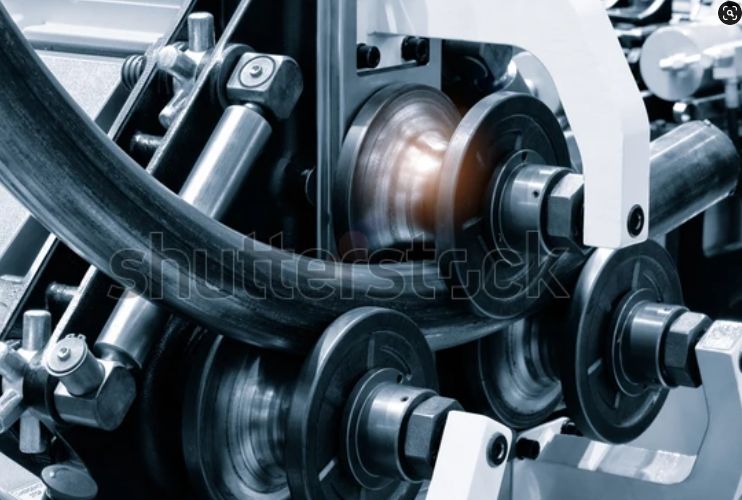
3. Efficient Welding Process
Next, the bending tube would be welding together automatically by the welding robots or welders. We have 25 welding robots, and 20 skilled manual welding lines. For batch orders, we will use robots for welding. For new design styles, due to the small number of early orders, we will perform manual welding.
Robots don't need to rest or rejuvenate like humans. They don't need to be shut down as often to generate working energy. As a result, robotic welding can operate at higher speeds for longer periods of time and, as a result, exceeds the output produced by human labor.
Robotic welding takes place in an enclosed area, which makes manual work difficult. As a result, humans do not need to remain in contact with the high temperatures and intense arc glare of the welding process, which greatly increases their safety in the work environment. On the other hand, injuries and damaged equipment can cost a company a lot.
Robotic welding is done pro-grammatically, so it is highly repeatable and improves output accuracy. It reduces all possible opportunities for human error throughout the operation.
The high level of precision allows the robot to create fewer gaps, and the amount of debris damaged in the process is greatly reduced. It also minimizes the level of human intervention, and companies can save money by hiring fewer employees.
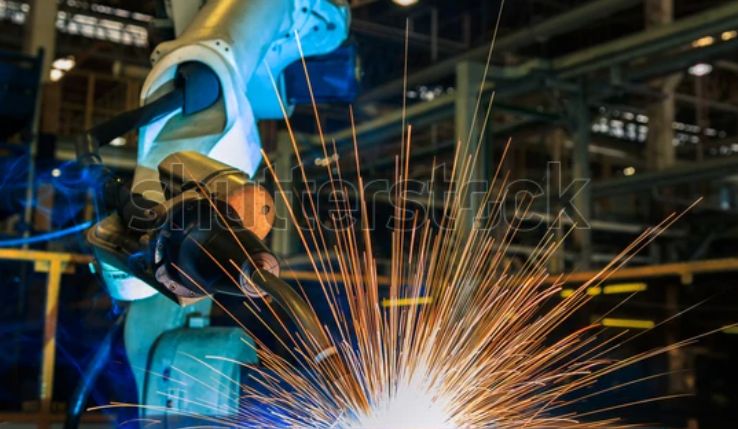
4. Grinding and polishing
Before do the finishing, especially for the manual welding, the frames will go through 2 times grinding and 2 times polishing by our experienced workers, which could make the welding parts smooth enough.And especially also a good basement of the chromed golden finishing. Even by reducing 1 time process, the burrs, the leak painting would appear on the surface of the legs.
5. Finishing the legs/Frames
The surface of the legs/frame is the final process. We could support powder coated painting,wood transfer,chromed,and golden chromed finishing to reach different customers demand.
Black powder coated painting is our main finishing for most upholstery chairs. And we finish the powder coated painting by 2 steps-acid pickling and hosphorization.
First, we will According to a certain concentration, temperature and speed, the metal legs or frames are pickling by acids remove iron oxide skin chemically,which ensure the smooth surface of the metal legs /frames.Next,we did the process of forming a phosphate coating on the metal surface through chemical and electrochemical reactions.The formed phosphate conversion film is called a phosphating film.At the same time, the phosphate film formed as a lubricating carrier has a good reaction with the lubricant and reduces the surface friction coefficient of the subsequent processing of the material. Improve paint adhesion and prepare for the next step.
Colorful frames also could be customized according to clients pointed Pantone colors.
6. Fabric/Faux leather cutting
After receiving the raw fabrics from suppliers, firstly we will compare it with the signed samples colors,If the color difference is really big, beyond the acceptance from our standard or customers’ requirements,we will return them to raw materials suppliers. If the color difference under control, We will put them on the automatic cloth cutting machine for cutting.The fabric is automatically spread and automatically cut into the required shape. At the same time, the cutting is accurate and the utilization rate of the fabric/faux leather is improved,while reducing labor costs.
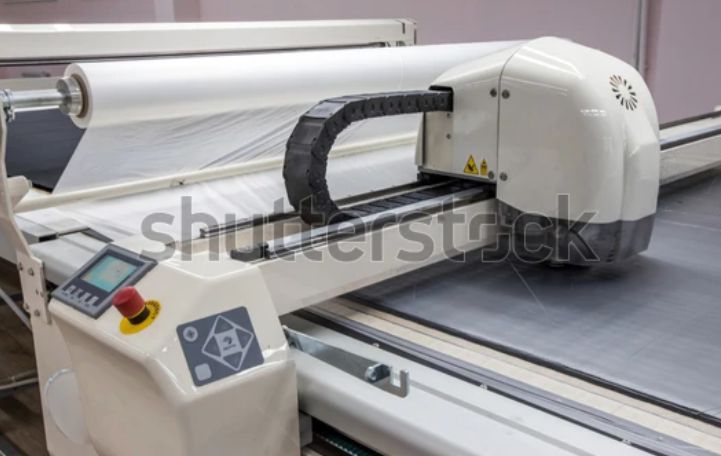
7.Diamond/Line stitching
For some diamond-shaped or smashed software, we will put it on the automatic quilting machine for quilting. Compared with the traditional manual sewing machine, it has the characteristics of fast speed and accurate quilting and embroidery.
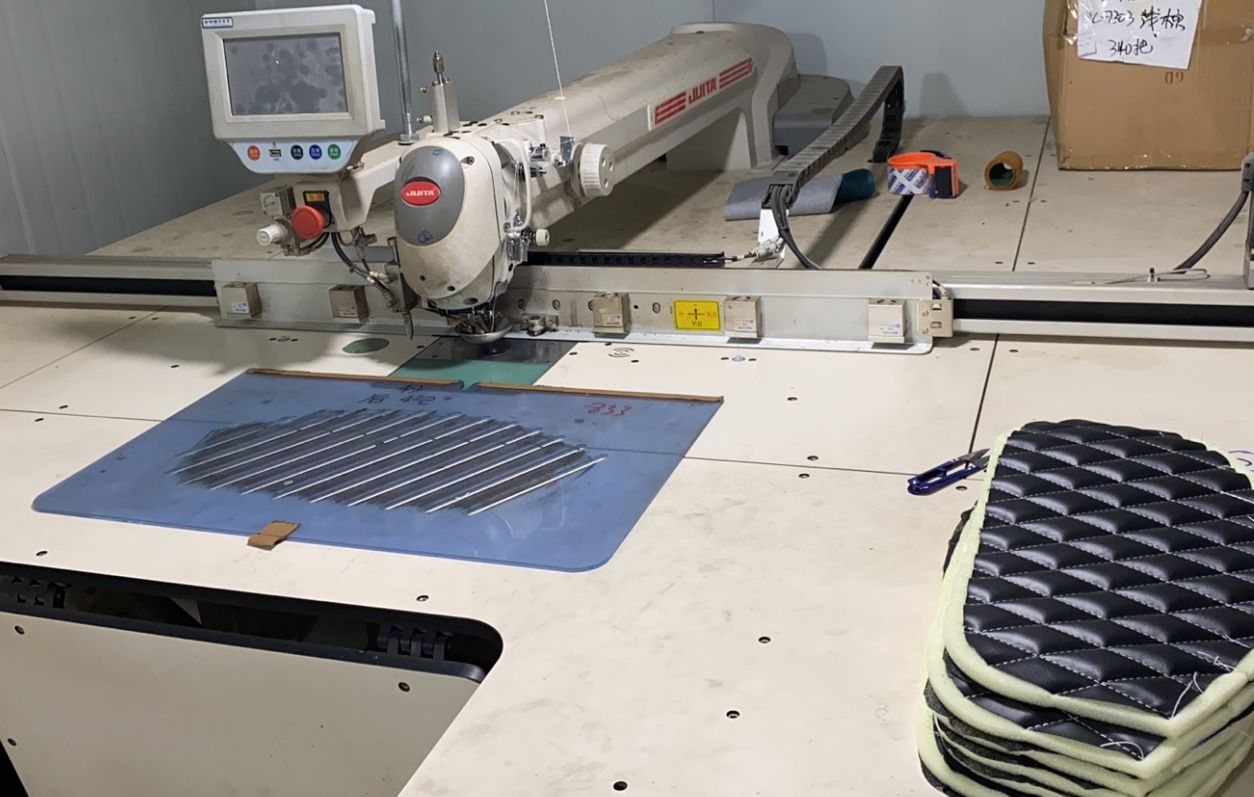
8. Make holes and nut on Plywood
When purchased plywood arrived at the warehouse, next step, we will punch the holes, bury the nut to prepare for pasting the sponge.
9. Spray glue and sticky sponge
With people's environmental awareness and environmental requirements in Europe, the United States and other countries, we all use environmentally friendly glues. In order to ensure that the product can pass the test of the relevant market. Such as the reach test in Europe. At the same time, the sponge can be better pasted on the plywood or metal frame seat and back to ensure long-term use without falling off.
10.Upholstery
Upholstery is according to customers' preference or marketing needs. Such as the density, thickness,resilience of the sponge,the fabric/faux leather type, if the seat or back with diamond/line stitching etc.Customers can choose the colour, material from our cooperated suppliers and/or supply their own. Just advise our the contact of the supplier would be ok.Our purchasing dept would contact them asap.
Our staff with 10 years of work experience, without exaggeration, can perfectly control the distance between each gun nail. Although it is at the bottom of the seat cushion, it is not sloppy.
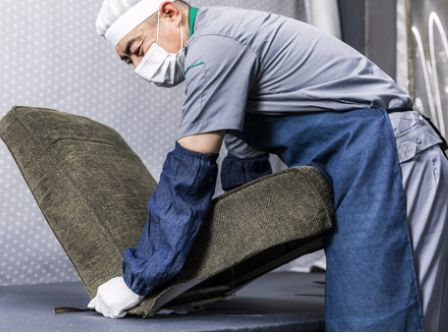
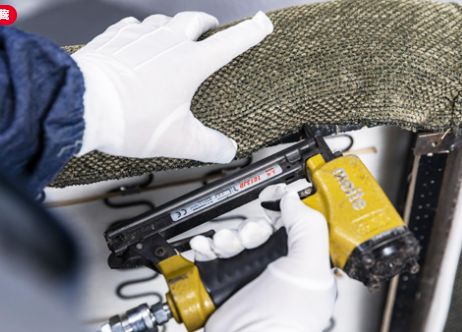
11. Finalisation
When finished legs surface,before assembling, our experienced staff will check each legs and adjust the four legs at same level to assure they are flat. And then , the legs and upholstery will be assembled and given their final shape.Till now, a exquisite workmanship upholstered chair is finished.
12. Packaging
After receiving the order from customers, the sales will send a guideline to customers and communicate and confirm a final requirements of the packages, or we will issue a package guideline to the packaging workshop director according to the detailed packaging requirements provided by the customers.And the packaging workshop will strictly follow the packaging guide to pack the chairs correctly. Specifically, whether the upholstery need to paste the labels,the labels words and label shape etc; law labels, hangtag, whether the PE bags need holes and printing words; whether the legs are protected by non-woven fabrics or PE cotton; the bags fixed by the hardware bag, and the location;The style and number of copies of the assembly instructions;Whether to put desiccant and so on. In order to ensure that the quality inspection of the goods has a basis, it is also an important guarantee to fully meet the requirements and expectations of customers.
13. Testing
Quality is the life for VENSANEA. Each upholstered chairs we produced are strictly checked at each manufacturing level by our QC team. Besides that, the finished chairs undergo specific strength and durability tests in our laboratory or the third party test centre,like TUV,SGS,BV,Intertek etc in accordance with the European standard EN 12520 – Strength, durability and safety . They withstand perfectly even the most demanding tests. That’s make each customers could wholesale or retail the chairs we made. Besides,each order we would random sampling from mass production to do the dropping test based on international standard,such as ISTA-2A, which could ensure the customers get the well packaged goods.
And chemical test also proceed by third party company, TUV,SGS,BV etc.
Such as REACH SVHC,TB117, Lead free painting powder etc.
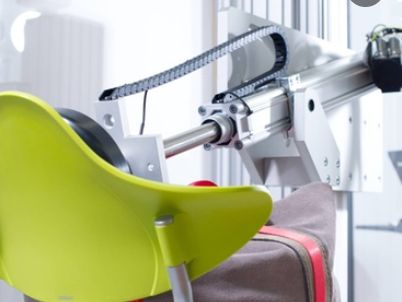
Post time: Nov-16-2023